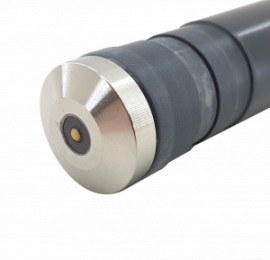
Why is there a requirement for peracetic acid (PAA) online monitoring?
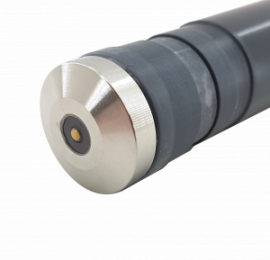
Common disinfectants such as chlorine and chlorine dioxide have been used effectively in water applications for over a century. Some industries however have looked to use other alternatives which have fewer or no considerations of safety and which don’t require residual or by-product removal. One of these alternatives, which has found increasing popularity across many industries, is peracetic acid (PAA). As more applications turn to PAA disinfection there has been an increase in demand for a reliable and accurate monitoring and dosing analyzer.
Process Instruments’ (Pi) PeraSense is a robust online analyzer capable of continually monitoring and optimizing the levels of PAA, providing you with the peace of mind that chemicals won’t be wasted and the water quality will never be compromised!
Did you know that…
…Pi’s PeraSense requires approximately ten minutes of maintenance, once every six months?
…Pi’s PeraSense is suitable for all potable, process and salt waters?
…Pi’s PeraSense amperometric sensor has up to a 15 year life span?
What is peracetic acid and why is it used?
PAA is a powerful oxidant with an oxidation potential, used as a measure of disinfection effectiveness, greater than that of common disinfectants such as chlorine and chlorine dioxide. It is produced by the reaction between acetic acid and hydrogen peroxide when dissolved in water, and degrades over time forming non-toxic water soluble products. The free radical degradants (bug killing species); hydrogen peroxyl and hydroxyl have high oxidizing capacities and are generally believed to destroy bacteria via the protoplasmic oxidation mechanism resulting in bacterial cell wall disintegration. The safe degradation pathway and high oxidation properties make PAA a popular disinfectant for many applications and industries.
Not only does PAA have greater disinfection power when compared to other alternatives but there are also implications of using chlorine which PAA users do not experience.
Chlorination of water can be achieved using three chemical mediums; chlorine gas, calcium hypochlorite and sodium hypochlorite, all of which have proved useful in many applications.
There are, however, several factors which affect their viability and all three mediums have safety concerns which must be addressed, including; potential gas release, corrosive properties and stability under heat and sunlight. As a result of this, sites often spend considerable amounts of time and money implementing safety precautions such as the safe generation and storage of these chemicals.
Furthermore, chlorine reacts with natural organic compounds found in the water supply forming potentially harmful disinfectant by-products such as Trihalomethanes (THMs) and Haloacetic acids (HAAs). The potential health hazards associated with exposure to these by-products, particularly THMs, have resulted in extensive drinking water regulations across the developed world with a stipulation on regular monitoring of these compounds across the water distribution system. As PAA usage only results in non-toxic degredants, no further costs are incurred on instrumentation to monitor potentially harmful residuals or by-products.
Although PAA does still have some safety considerations, as with all disinfectants, it is widely accepted that storage, generation and stability is superior to using chlorine.
What are the typical applications PAA is used for?
PAA has been primarily used as a cleanser and disinfectant in the food industry since the 1950s, particularly for fruit and vegetable washing due to its highly effective anti-microbial properties. All disinfectants applied directly to food must not leave harmful residual by-products, which is why PAA is so widely used in this industry around the world. Other industries in which the water cleanliness is of paramount importance have also turned to PAA for disinfection including; agricultural, dairy processing, wineries, breweries and even cooling towers.
Pi’s work with H&M Disinfection – Food and Beverage Disinfection
H&M Disinfection have designed, manufactured and installed cleaning and disinfection systems for the Food, Dairy and Beverage industries since the late 1980’s, providing their customers with bespoke cleaning solutions specific to their clients needs. More recently, Pi and H&M Disinfection combined their experience and expertise in water quality monitoring instrumentation and disinfection process engineering respectively to supply a UK food processing plant with an optimum water treatment solution, capable of handling their peak process water demand to ensure the sites final water meets the industry’s strict regulations. Pi’s peracetic acid analyzer made up a small but integral part of the water treatment system provided by H&M Disinfection and continues to ensure the customer has optimum water quality.
Fundamentally, an effective PAA chemical dosing controller should allow the user to find the perfect balance between saving PAA and dosing enough for optimum disinfection and this relies on the quality of the instrumentation. Pi’s PeraSense is the complete PAA dosing controller which uses a state of the art two electrode amperometric sensor to provide the highest levels of accuracy for process PAA monitoring.
The controller provides the flexibility to ensure you have all the functionality you need and nothing which you don’t. The CRONOS® and CRIUS® controllers have up to two and four sensor inputs respectively, with the option of up to 16 sensor inputs with expansions on the CRIUS® meaning you can monitor multiple parameters from a single controller.
The PeraSense has the option to come with full PID and output controls, which are completely user configurable to provide the site with the ability to make the instrumentation suit their needs. Pi’s controllers can also offer the option for remote access, which provides site or servicing contractors the ability to remotely monitor the live levels of PAA, trend historic data, view system alarms, remotely configure settings and much more.